/https%3A%2F%2Felbilen.se%2Fwp-content%2Fuploads%2F2021%2F02%2FNorthvolt-Labs-Aug-2020.jpg)
Emma är hjälten bakom Northvolts batteriåtervinning
/https%3A%2F%2Felbilen.se%2Fwp-content%2Fuploads%2F2023%2F03%2FLotta-kopiera.jpg)
Lotta Hedin
21 feb 2021
Att använda uttjänta elbilsbatterier för att tillverka nya är en viktig del i Northvolts affärsidé – om tio år ska hälften av råmaterialen i de batterier som företaget tillverkar komma från återvunnet material. Vägen dit leds av miljöchefen Emma Nehrenheim, som nu fått pris för arbetet med Northvolts återvinningssatsning Revolt.
Text: Lotta Hedin. | Foto: Northvolt.
Svenska batteritillverkaren Northvolt siktar på att lägga under sig en fjärdedel av marknaden för elbilsbatterier i Europa. Hälften av råmaterialen som behövs i dessa ska komma från återvunnet material, enligt företaget. Men för att det ska bli möjligt måste Northvolt snabbt säkra ett inflöde av uttjänta batterier, och etablera ett effektivt och lönsamt sätt att ta vara på innehållet i dem. Det är just det som Emma Nehrenheim och hennes kollegor arbetar med i företagets återvinningsprojekt Revolt.
Enligt stiftelsen Skapa, som delar ut Sveriges största innovationspris, är det ett arbete väl värt att uppmärksamma. Emma Nerenheim tilldelades nyligen priset ”Skapa-förebild”, vars syfte är att lyfta fram hjältarna bakom kulisserna.
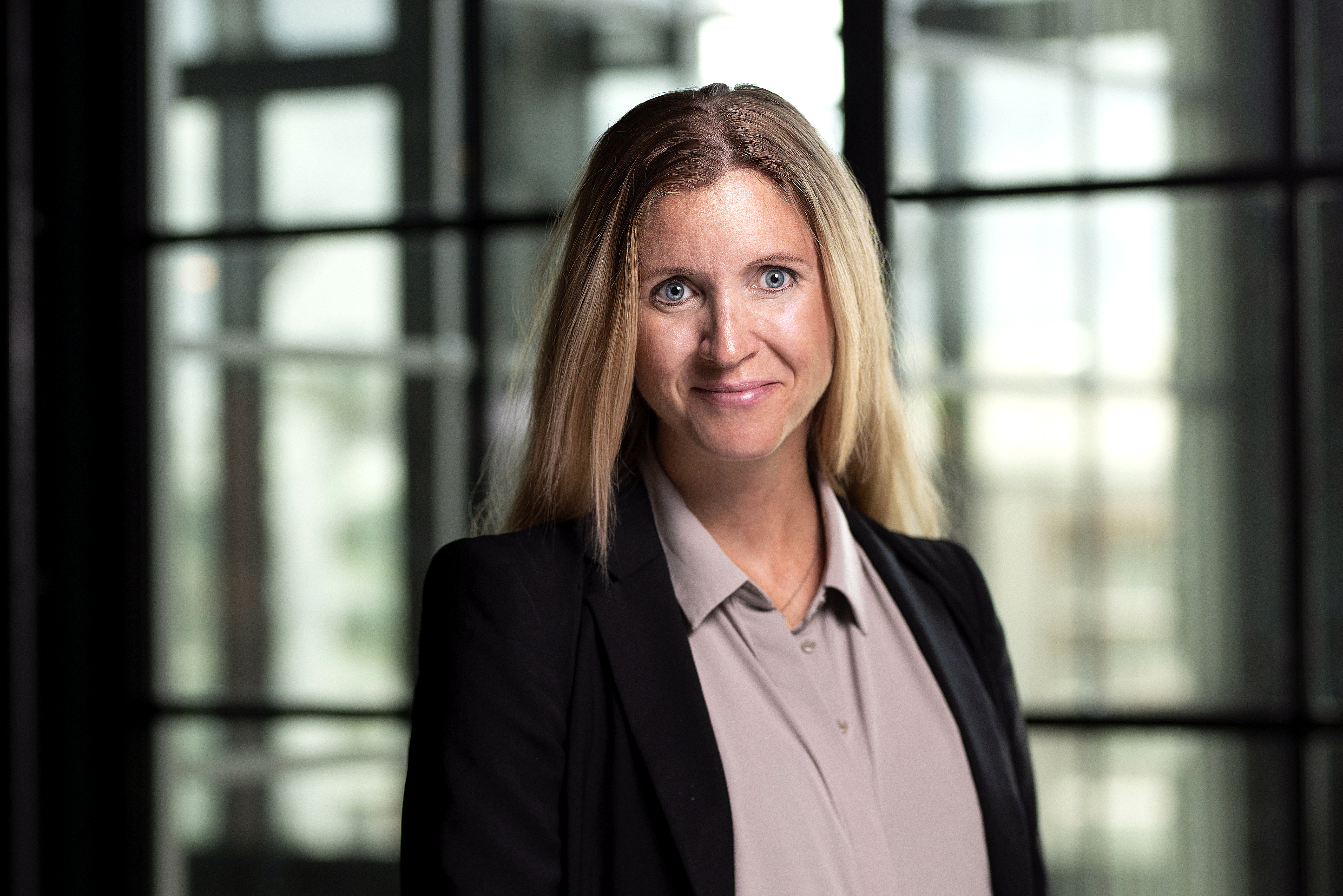
”Emma och hennes team arbetar med en process som beräknas bidra till att återvinning av batterier möjliggörs i industriell skala. Processen kommer därmed att bli en avgörande insats för miljön. Inget av detta hade varit möjligt utan Emmas ledarskap och vision”, skriver juryn i motiveringen.
– Det är svårt att identifiera sig med så stora ord, vi är ju ett helt team. Alla som har varit med på den här resan har lagt så otroligt mycket tid och engagemang, säger Emma Nerenheim.
Arbetet med att ta fram processer för återvinning började 2017, samma år som Emma Nehrenheim kom till Northvolt. I somras öppnade man en pilotanläggning i Västerås där hela återvinningskedjan testas, från urladdning och uppackning av förbrukade batteripack, till att rena grundämnen utvunnits och är klara att användas på nytt i nya celler.
Pilotanläggningen ska sedan stå modell för en fullskalig återvinningsanläggning som ska byggas i anslutning till Northvolts fabrik i Skellefteå, som ska tas i drift 2022. Northvolt har också inlett ett återvinningssamarbete med norska Hydro. En gemensam anläggning ska byggas i Norge 2021.
– Syftet med den här anläggningen är att skapa en tydlig färdighet, både för anläggningen vi bygger i Norge, i Skellefteå, men också för att förbereda, testa och prova inför nästa typ av samarbeten. Vi ser framför oss att vi kommer ha nära samarbete med kunderna på de tidiga stadierna i återvinningskedjan längre fram, säger Emma Nerenheim.
Redan nu är återvinningen i full gång vid pilotanläggningen.
– Vi kör för fullt. Vi har alla processteg under ett tak och kör alla delar. Vi har redan fått ut material som kan användas på nytt. Nästa steg är att göra färdiga celler av det, för att få ett så kallat proof och concept – ett bevis på att vi kan sluta hela cirkeln. Jag tror vi kommer ha dem klara någonstans kring nyår – möjligen under januari, säger Emma Nerenheim.
Stegen från uttjänt batteri till att alla råmaterial tagits tillvara är dock många. Till att börja med handlar det om att samla in bilarna och batteripacken. Sedan att ladda ur dem, och därefter packa upp batteripack och moduler. I nästa steg krossas materialet och koppar, aluminium, stål, plast, med mera, sorteras ut. Efter det återstår det som kallas för en svart massa, bestående av nickel, mangan, kobolt, grafit och magnesium. Materialen i massan skiljs sedan ut genom kemisk bearbetning, i en så kallad hydrometallurgisk process.
På det sättet kan 95 procent av nickel-, mangan- och koboltinnehållet återanvändas. Sett till hela batteripacket kan 90 procent av materialet återvinnas, enligt Northvolt.
Var ligger den största utmaningen i återvinningskedjan?
– Initialt upplevde alla på marknaden att det var att få finanserna på rätt sida om strecket när det gäller den hydrometallurgiska processen, som upplevdes så kostsam, om man skulle få materialet så rent som det är tvunget att vara. Men nu, efter att ha lagt två-tre år på att utveckla processen, har vi nått en hög effektivitet, så den tröskeln har vi klivit över. Nästa steg är de tidigare stadierna, att få hög effektivitet och säkerhet i insamlingen. Efter att batterierna samlats in behöver de snabbt laddas ur och tas isär så att de inte riskerar att vara skadliga. Det behöver man sätta processer för, och det behövs aktörer som har kunskapen och som klarar av att göra detta i stora volymer.
En utmaning är också att batteripacken ser helt olika ut i olika bilar, vilket gör det svårt att automatisera isärplockningen.
– Man får jobba sig igenom pack för pack. Vi prioriterar just nu våra egna kunders batteripack. Det är där vi har starka samarbeten och det är där vi ser att det kommer komma stora volymer tillbaka till oss tidigt.
Återvinningsanläggningen i Skellefteå ska ha kapacitet för att återvinna 25 000 ton battericeller årligen.
Nyckeln är egentligen processkunskap. Det jag brinner för är återvinning av alla värden som kan finnas i en industriell process.
Elbilar och batterier har hittills visat sig hålla längre än vad många först trodde. När kommer de stora volymerna av uttjänta batterier?
– Vi brukar säga att ungefär 10–15 år kommer batterierna finnas på marknaden, i normalfallet. Men det kan variera. Vi kommer ju även ha bilar som används i poolsystem, och för dem kommer tiden kanske vara något kortare eftersom de används mer.
– Om 10–15 år tror jag vi har kommit till det jag kallar för steady-state, då vi kommit till ett 1 till 1-flöde, alltså ett batteri ut på marknaden och ett batteri tillbaka. Men det kommer finnas stora behov av återvinning före det.
Emma Nehrenheim har en doktorsexamen i miljö- och energiteknik, och var tidigare verksam som forskare och professor vid Mälardalens högskola. Året innan hon började arbeta på Northvolt, 2016, fick hon pris av kungen för ett projekt om mikroalger i framtidens reningsverk.
Hur kom det sig att du gick därifrån till batterier?
– Nyckeln är egentligen processkunskap. Om man går tillbaka lite längre – i mitt exjobb tittade jag på återvinning av ammunition, och jag gjorde min avhandling om återvinning av masugnsslagg. Sedan har jag tittat på återvinning av barkflis. Därefter kom algprocessen in, för det är så frustrerande att vi slösar bort så mycket näringsämnen som vi gör ur avloppsvattnet.
– Det jag brinner för är egentligen återvinning av alla värden som kan finnas i en industriell process. En produktionsprocess som genererar en ström med värdefullt material, men också genererar mycket avfall som bara slängs – det är inte ett sätt som vi kommer klara av att jobba på i framtiden. Man behöver hitta cirkulariteten, både i samhället och industrin.
– Och det ska man komma ihåg när det gäller batterier: den huvudsakliga skillnaden mellan ett litiumjonbatteri och en bil med förbränningsmotor är att batteriet kan återvinnas. Så länge batteriet hela tiden laddas med förnybara källor och produceras förnybart så finns det en teoretisk grund för ett hundra procent cirkulärt flöde. Det är en fundamental skillnad mot en förbränningsmotor, där oljan per definition kommer pumpas upp, raffineras, tankas i bilen och bli till en gas som går till atmosfären. Det spelar ingen roll vilka livscykelanalyser man gör. När man kommer till förbränningsmotorn kan man inte komma längre än vad vi har kommit i dag. Medan när det gäller batterier så kan vi ta oss hela vägen ut till ett hundra procent cirkulärt flöde, om vi bara gör jobbet.